コスト低減・効率化をご提案
物流技術管理士等が親身にご相談に乗ります
お客様が物流業務に対して疑問をお持ちだったり、新たに物流の仕組みを模索されている際に、物流技術管理士等が親身に御相談に乗り、これまでの弊社実績と物流業務をトータル的に捉えることにより、コスト低減・効率化をご提案致します。
ご提案までの流れ
1.弊社への問合せ
まずは、お問合せください。(お問合せフォーム または電話にて)
物流に関する疑問・質問
どんなことでも構いません。
2.お客様をご訪問
お問合せ頂いたお客様のもとへ、営業担当者がお伺い致します。
ここで、お客様がお困りの内容をお聞かせ頂きます。
物流関連の情報(現状・計画)を詳細に御提示頂くことにより、より精度の高い業務改善をご提案出来ます。
また、倉庫管理等については、実態調査(ワークサンプリング)等を実施させて頂き、業務提案に繋げさせて頂きます。
3.業務提案作成
弊社内で総力を挙げ、現状分析・改善点を模索し、ベストな業務提案を検討致します。
4.業務提案ご説明
お客様より御提示頂いた情報・弊社にて調査させて頂いた情報を基に作成した業務提案をご説明致します。
ここでご説明した内容を基に、より具体的な実施方法・時期等の御打合せを進めさせて頂きます。
5.詳細御見積り御提示
弊社への業務発注により、詳細見積りを御提示致します。
6.業務開始
十分な準備、教育を行い、業務を開始致します。
運送改善提案例
改善提案の一例として、運送に関する改善を図示します。
改善前
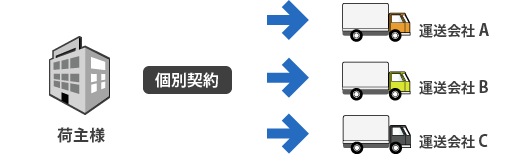
荷主様と複数運送会社が個別契約し、車輌手配を荷主様物流担当が行い、夫々の運送会社で運送業務を実施。(非効率配車)
使用車輌単価で料金発生 輸送コスト増加
改善後
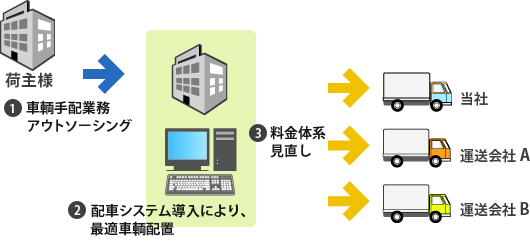
- 荷主様より車輌手配(配車)業務をアウトソーシング
- 配車システムを導入し、自車輌・協力会社車輌を最適配車(効率化)
- 料金体系の見直し(チャーター料金制→従量料金制)など
配車業務アウトソーシング 荷主様 本来の業務に専念
車輌配送効率向上・料金体系見直し 輸送コスト削減
倉庫管理改善提案
改善提案の一例として、倉庫管理に関する改善を図示します。
改善前
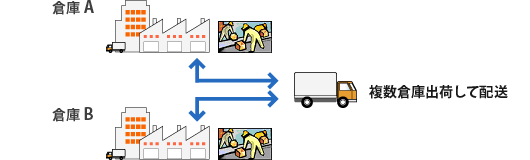
- 倉庫入出庫作業:複数倉庫での作業→作業人員増(無駄)
- 商品配送:複数倉庫への集荷→車輌増(非効率)
- 商品管理:煩雑→一元化出来ず、在庫棚資産増(無駄)
無駄・非効率の積算 倉庫管理コスト増加
改善後
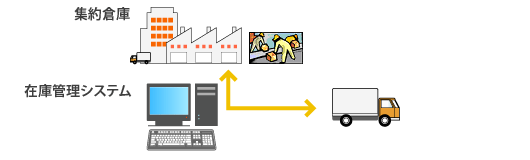
- 荷主様より倉庫管理(入出庫・在庫)業務をアウトソーシング
- 倉庫集約により人件費削減(倉庫賃貸料削減)
- 在庫管理システムを導入し入出庫処理(格納・ピッキング)を効率化
- 在庫管理システムによる出庫品質向上(誤出荷防止)
- システム管理された在庫→最適在庫での倉庫棚資産削減 など